

Research Area
Advanced High-Strength Steels Design

For the past decades, the automobile industry has been improving fuel efficiency, passenger safety, and reduction in greenhouse gas emission by adopting advanced high strength steels (AHSS) with both high strength and high ductility. In general, AHSS is classified as the first-generation AHSS (1st-G AHSS), the second-generation AHSS (2nd-G AHSS), and the third-generation AHSS (3rd-G AHSS).
The 1st-G AHSS, such as dual-phase (DP), complex-phase (CP), and transformation-induced plasticity (TRIP) steels, possesses the high strength of over 600 MPa but the relatively low ductility of below 20%. This low ductility restricts the application of the 1st-G AHSS to automobile parts with complex shapes. The 2nd-G AHSS, such as high Mn TRIP and twinning-induced plasticity (TWIP) steels, shows a remarkable combination of high strength of over 700 MPa and large uniform ductility exceeding 50%. The extraordinary tensile properties of the 2nd-G AHSS result from the high strain hardening rate due to the formation of strain-induced martensite or mechanical twins in the austenite phase during plastic deformation. However, the 2nd-G AHSS has difficulties in mass production, material cost, and welding, which are caused primarily by a lot of alloying elements greater than approximately 17 wt.%. Therefore, nowadays, the 3rd-G AHSS, such as lightweight steel, quenching and partitioning (Q&P) processed steel and medium Mn steel has been attracted because it has a good trade-off between material cost and mechanical properties.
One of the objectives of LAMP is to investigate the next generation AHSS showing better mechanical properties than 3rd-G AHSS even maintaining reasonable materials cost. This concept is based on optimal using of various strengthening mechanisms simultaneously.
Recycling-oriented Steel Design

To successfully transition to a carbon-neutral society, it is essential to decarbonize the industrial sector, which emits large amounts of greenhouse gases and is heavily reliant on carbon and energy. In particular, the steel industry is a highly carbon-intensive industry that emits significant amounts of greenhouse gases during its production process. Globally, the steel industry accounts for 7% of total greenhouse gas emissions and 25% of industrial emissions. In South Korea, the steel industry's greenhouse gas emissions constitute 13% of the nation's total emissions and 39% of industrial emissions, which is higher than the global average. Considering the steel industry's status as a key driver of South Korea's industrial development and the steady increase in demand for steel due to industrial advancement (1-2% annual growth, with global demand expected to reach approximately 2.747 billion tons by 2050), decarbonizing the steel industry is seen as an essential task.
The high greenhouse gas emissions from the steel industry primarily stem from the blast furnace-based manufacturing process, where coke is used as a reducing agent and reacts with iron ore to produce steel (for example, producing 1 ton of steel emits approximately 2 tons of CO2). As a solution to this problem, hydrogen reduction steelmaking has been proposed, which uses hydrogen as a reducing agent and emits no greenhouse gases. However, commercializing reduction furnaces to replace blast furnaces and producing green hydrogen as a coke substitute are expected to take considerable time and involve numerous trials and errors. In the meantime, the "Electric Arc Furnace Process Based on Steel Scrap Recycling," which can reduce greenhouse gas emissions by over a quarter compared to the blast furnace-based process, is gaining recognition as the most viable decarbonization alternative.
However, even apart from the burden of electricity costs in the manufacturing process, electric arc furnaces have several critical disadvantages compared to blast furnaces. Firstly, the blast furnace process allows for easy control of alloying elements, enabling the production of various high-value steel products for different uses. In contrast, the electric arc furnace process, which recycles steel scrap of varying compositions, struggles to adjust alloying elements, resulting in a limited range of products and lower profit margins (e.g., bars, rebar). Furthermore, tramp elements, which are difficult to remove during the scrap refining process, accumulate within the steel through repeated recycling cycles, degrading its mechanical properties and making it challenging to produce high-quality steel. Thus, overcoming these challenges is essential for successfully establishing an electric arc furnace production system based on steel scrap recycling.
In light of this, the current research project aims to develop a recycling-oriented, sustainable, environmentally-friendly variable-property steel material (REUSES: REcycling-oriented Uni-Steel for Environment and Sustainability) to support the establishment of an electric arc furnace production system.
1. Single-Composition Steel: The developed material has a single composition, yielding a uniform scrap composition, making it highly conducive to recycling and reproduction.
2. Variable-Property Steel Based on Microstructure Design: Through extreme control technologies for the microstructure, such as Thermo Mechanical Process (TMP) that influences element redistribution and phase transformations, the developed material can exhibit diverse properties despite its single composition. This allows it to be applied to various high-value steel products and components with opposing properties, using a single material. In contrast to conventional steel materials, which achieve the desired properties through changes in the alloy's chemical composition via a Chemistry-dominated Alloy Design, this research pursues a Microstructure-dominated Alloy Design, where the steel's broad range of properties relies more on microstructure control than on the alloy's chemical composition.
3. Damage-Tolerant Microstructure: Through extreme microstructure control technologies based on TMP, the developed material has a microstructure resistant to damage (Damage-Tolerant Microstructure), enabling excellent performance even in extreme environments such as cryogenic and hydrogen embrittlement conditions.
4. Tramp Element Resistance: Through a physical metallurgical study of tramp elements that negatively impact the properties of recycled steel (e.g., Cu, Sn, P), we aim to develop a material that exhibits minimal mechanical degradation even with high concentrations of these elements.
Advanced Alloys Design
Self-Healing Alloys
Superplastic Alloys

We also have a lot of attention to investigate multi-functional alloys such as self-healing alloy, multi-component alloy (high entropy alloy), Ti alloy, and cost-effective superplastic alloy. The objective of the research scheme is to develop not only alloys with excellent sustainability for extreme environments but also unraveled phenomena of alloys to suggest novel routes for the application such as hydrogen-storage metal, nuclear material, and thermoelectric material.
Low CTE & High Strengh/Toughness Alloy Design for Aerospace Applications

To manufacture structures exposed to the extreme conditions of space, such as satellites and space shuttles, it is essential to develop alloys that simultaneously offer lightweight properties, low thermal expansion, high toughness, and high strength in the temperature range of -200 to 100°C. For example, the Invar alloy, currently used for connector components, features high toughness and low thermal expansion. However, due to its high density and low strength, it is challenging to use this alloy alone for manufacturing space structure components. In this study, we are investigating the potential of creating a single alloy for space structure components by using the Clad process to develop alloys that simultaneously satisfy various required properties.
Failure Analysis
Hydrogen Embrittlement

Hydrogen is known to be one of the most harmful elements in steel because the presence of that in steels might cause a detrimental effect on mechanical properties. The hydrogen can permeate in steels from the production process (e.g. pickling, electroplating, and welding), product assembling, and service environment exposure. Even a very low concentration of hydrogen (less than 1 ppm) can cause a significant decrease in ductility and premature failure of steels and this phenomenon is the so-called hydrogen embrittlement (HE). It is known that the diffusible hydrogen is the suspect causing HE, and there are several proposed mechanisms for HE, such as internal pressure model, hydrogen-enhanced decohesion (HEDE), hydrogen-enhanced local plasticity (HELP) and hydrogen-enhanced strain-induced vacancy (HESIV).
Our lab.`s objective is to clarify the HE mechanism of alloys with various microstructures and showing various deformation mechanism like TRIP and TWIP through the state-of-the-art analyses by thermal desorption analysis (TDA), scanning Kelvin probe microscope (SKPFM) and post-mortem microstructural analysis such as electron backscattered diffractometer (EBSD) and electron channeling contrast imaging (ECCI) method. Through our research, we expect to reveal the reason for HE in steels.
Low-Temperature Embrittlement

With decreasing the environment`s temperature, the alloy`s fracture mode sometimes changes from ductile fracture to brittle fracture, and this phenomenon is so-called as ductile to brittle transition. The various factors could affect the ductile to brittle transition behavior such as crystal structures, lattice defects, and element segregations.
Our lab.`s objective is to clarify the low-temperature embrittlement mechanism of alloys and suggest the solution for improved mechanical responses through post-mortem analyses using combined EBSD/ECCI techniques and segregation engineering using STEM-EDXS and 3D atom probe tomography (APT).
Thermo-Mechanical Process Design
Resetting process

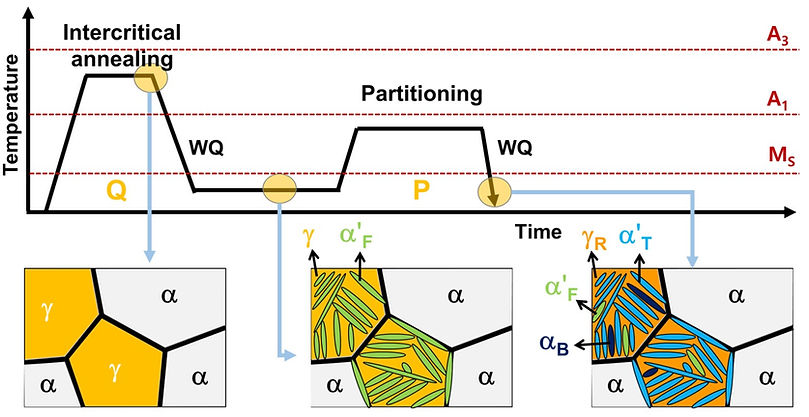
QLT process

Advanced QLT process
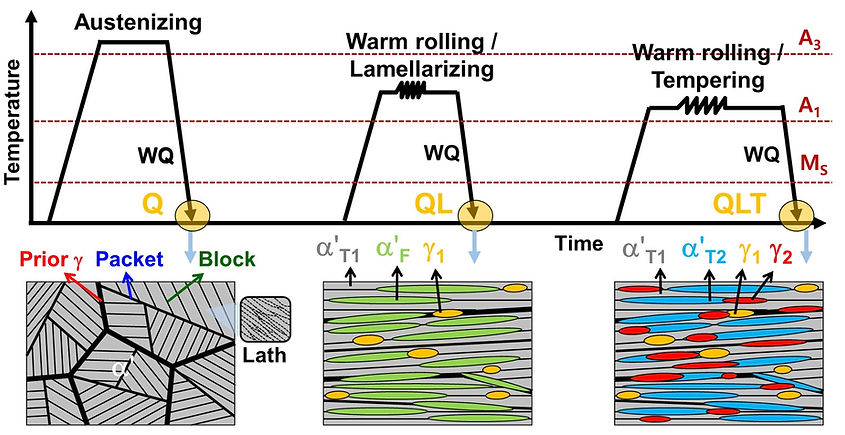
The microstructure of alloys and steels could be controlled by the material`s synthesis. Generally, alloys are subjected to various hot and cold rolling or forging and annealing with various conditions for the productions. This procedure is called as a thermo-mechanical process. The different microstructures which are characterized by various thermo-mechanical process give a lot of effort on material`s properties such as mechanical properties.
Our lab`s goal is to try and apply the various thermo-mechanical process on various alloys and steels to optimize the mechanical properties.
Multi-Scale Microstructure Analysis

Revealing interrelation between microstructure and mechanical properties is the essential topic of the metallurgical engineering. Multi-scale microstructural analysis from bulk scale to atomic scale could give a clear information of the component of steel and alloys, thus it could facilitate the successful alloy design and reveal the secret of interrelation.
Our lab uses state-of-the-art microstructural analysis techniques such as not only general X-ray diffraction (XRD) and electron microscope (SEM, TEM), but also high-performance electron backscatter diffraction (EBSD), electron channeling contrast imaging (ECCI) and 3D atom probe tomograph (APT).
Research Projects
On-going projects

01. April. 2024 - 31. March. 2028
LAMP is funded by NRF from April. 2024 to March. 2028. Topic is "Development of REcycling-oriented Uni-Steel for Environment and Sustainability(REUSES) through Microstructure-dominated Alloy Design".
01. December. 2023 - 28. February. 2027
LAMP has been designated as 4th Hyundai Steel Research Lab. The research topic is related to the development of innovative steels for cryogenic hydrogen environments and 3rd generation advanced high strength steels.

01. August. 2023 - 31. December. 2027
LAMP is funded by NRF from August. 2023 to December. 2027. Topic is "Breakthrough Trade-off Properties in Metallic Materials for Satellite Applications through Multiformity Integration Novel Design (MIND)".

01. July. 2023 - 31. December. 2027
LAMP is funded by MOTIE from July 2023 to December 2027. Topic is "Development of design for additive manufacturing technology and low alloy steel materials with tensile strength 1.0 GPa for next-generation components".

01. March. 2023 - 28. February. 2028
LAMP is funded by MOTIE from March. 2023 to February. 2028. Topic is "Expert Training Project for the eco-friendly metal material industry".

01. September. 2021 - 31. December. 2025
LAMP is funded by NRF from March. 2022 to December. 2025. Topic is "Development of thermomechanical processing technology for Fe-Ni Invar alloy foils fabricated by electroforming".
Finished projects

02. May. 2024 - 31. July. 2025
LAMP is funded by Hyundai Motors from May. 2024 to July. 2025. Research objective is to investigate the superplasticity of lightweight Mn-bearing steels.

01. April. 2024 - 31. March. 2025
LAMP is funded by Hyundai Motors from April. 2024 to March. 2025. Research objective is to suggest the suitable electro-chemical charging methods for hydrogen embrittlement for the development of structural materials for hydrogen storage system.

01. April. 2021 - 31. December. 2024
LAMP is funded by MOTIE from April. 2021 to December. 2024. Topic is "The Development of high-performance 80ksi hot rolled material manufacturing technology with excellent HIC corrosion resistance".

01. July. 2023 - 31. March. 2024
LAMP is funded by Hyundai Steel from July 2023 to March 2024. The research theme is related to the embrittlement and mechanical properties of martensitic steels.

01. February. 2023 - 30. November. 2023
LAMP is funded by Hyundai Motors from February. 2023 to November. 2023. Topic is "Unraveling the effect of tramp elements for eco-friendly steel design".

01. February. 2023 - 30. November. 2023
LAMP is funded by Korea Shipbuilding & Offshore Engineering from February. 2023 to November. 2023. The topic is "Unraveling the hydrogen embrittlement mechanism of commercial steels for cryo-hydrogen environments".

01. December. 2022 - 30. November. 2023
LAMP is funded by Hyundai Steel from December. 2022 to November. 2023. The research theme is related to the development of new steel for cryogenic hydrogen environment.

16. May. 2022 - 15. November. 2022
LAMP is funded by Hyundai Motors from May. 2022 to November. 2022. Topic is "Development of micro-DIC measurement technique to predict the formability of automotive steel sheets".

01. April. 2021 - 31. May. 2024
LAMP is funded by MOTIE from April. 2021 to December. 2023. Research theme is "Development of eco-friendly heat treatment process technology to enhance the quality of steel components".

01. April. 2021 - 31. December. 2021
LAMP is funded by Korea Shipbuilding & Offshore Engineering from Arpil. 2021 to December. 2021. The topic is the investigation of low-Ni steel with excellent cryogenic impact toughness.

01. June. 2020 - 28. February. 2023
LAMP is selected as a laboratory for "Basic Research (기본연구)" of NRF. The research theme is "Ultrahigh strength lightweight maraging armor steel". Our goal of this project is to design bullet-proof maraging steel by rendering of nanolaminate morphology and dynamic strengthening mechanisms.

01. February. 2020 - 31. July. 2020
LAMP is funded by Korea Shipbuilding & Offshore Engineering from February. 2020 to July. 2020. The research theme is the investigation of medium-Mn steel with excellent cryogenic impact toughness.

01. January. 2020 - 31. December. 2021
LAMP is funded by POSCO TJ Park Foundation from January. 2020 to December. 2021. The research theme is designing new-era steel to overturn a conventional physical metallurgy theory.

01. March. 2018 - 28. February. 2023
LAMP is selected as a laboratory for "Metal Expert Training Project for High-value added metal material (고부가 금속소재 전문인력양성사업)" of MOTIE. The project period is from Mar. 2018 to Feb. 2023 and research theme is discovering new concepts of alloy design for next-generation high strength steels, the special phenomenon of steels (e.g., hydrogen embrittlement, low-temperature toughness, etc.).

01. June. 2018 - 31. May. 2019
LAMP is funded by Hyundai Steel from June. 2018 to May. 2019. The research theme is related to the mechanical response of advanced high strength steels.

01. March. 2018 - 31. December. 2018
LAMP is selected as a laboratory for "Research Funding for Cooperative Research" of KBSI. The project period is from Mar. 2018 to Dec. 2018 and research theme is "Unravelling reverse transformation mechanism and deformation behavior at a high temperature of medium Mn steel".

01. March. 2017 - 28. February. 2020
LAMP is selected as a laboratory for "Research Funding for Starting Professor (신진연구자지원사업)" of NRF. The project period is from Mar. 2017 to Feb. 2020 and research theme is "Investigation on Multifunctional Medium Mn Lightweight Steels with Giga Strength". Our goal of this project is to design cost-effective modern AHSS with lightweightness, high resistance to hydrogen embrittlement and low-temperature embrittlement.